Зносостійкий сплав
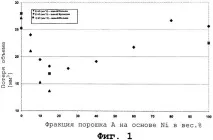
Власники патенту UA 2530196:
Винахід відноситься до галузі металургії, а саме до зносостійкого сплаву, що використовується для отримання формованих продуктів, відлитих продуктів, покриттів, дротів, електродів, порошків і сумішей. Сплав містить від 13 до 16 вагу. відсотків нікелю (Ni), від 13,5 до 16,5 вага. відсотків хрому (Cr), від 0,5 до 3 вага. відсотків молібдену (Mo), від 3,5 до 4,5 вага. відсотків кремнію (Si), від 3,5 до 4 вагу. відсотків бору (B) та від 1,5 до 2,1 вага. відсотків вуглецю (C), залишок – залізо (Fe). Забезпечуються високі зносостійкість та хімічна стійкість за низької вартості. 15 з.п. ф-ли, 3 іл., 3 табл., 1 ін.
Даний винахід стосується матеріалу, що містить сплав на основі заліза, що включає C, B, Cr, Ni, Si та Мо.
Матеріал або сплав можна застосовувати для отримання формованих продуктів, відлитих продуктів, покриттів, деталей, покритих деталей, дротів, електродів, порошків та порошкових сумішей.
Відомий рівень техніки
У промисловості існує потреба у сплавному матеріалі, що має відмінну стійкість до зносу та корозії та з низькою вартістю.
Застосування сплавів на основі нікелю з добавками хрому та молібдену для отримання захисту від зносу та корозії було давно відоме. Такі сплави розкриті, наприклад, у патентах США №№6027583 А, 6187115 А та 6322857 А.
У європейській заявці ЕР 1788104 А1 розкривають матеріал для виробництва деталей або покриттів, адаптованих для швидкого зношування та застосування з інтенсивним тертям. Матеріал містить метал на основі нікелю з добавкою твердих частинок, таких як WC.
Елементи Ni та W є дорогими, і розшукуються альтернативи.
Самоплавкі сплави на основі заліза є альтернативною групоюматеріалів з низькою вартістю, і виявили багато матеріалів, які виявляють помірну зносостійкість.
Такий сплав на основі заліза відомий із патенту Німеччини DE 19733306 C1. У ньому розкривають термічний матеріал, що покриває, на основі заліза. Сплав застосовують як додатковий матеріал у формі суміші, сплаву з розпиленим газом, агломерованого металевого порошку, дроту із заповненням між жилами, стрічки із заповненням між жилами, спеклої стрічки або відлитого обшитого стрижневого електрода і застосовують для термічного покриття компонентів, які піддаються трену. Переважною композицією сплаву для нанесення шару з низьким тертям і низькою стійкістю для компонента ковзання в поєднанні з хорошою витривалістю та міцністю ударів є наступна (за вагою): 20-25% Mn, 13-20% Cr, 0,1-2% Ni, 3 -6% W, 0,1-0,15% C, 1,5-2,5% B, залишок – Fe. Іншою кращою композицією сплаву для нанесення шару з низьким тертям з високим опором стирання і більш високим термічним навантаженням є наступна (за вагою): 18-25% Mn, 13-25% Cr, 0,1-2% Ni, 3-5 % W, 0,1-0,15% C, 4-6% B, залишок – Fe.
У патенті Німеччини DE 19901170 А1 розкривають інший сплав заліза з високими вмістами вуглецю, бору, ванадію, хрому, молібдену та нікелю. Запропонували наступну композицію (за вагою): 2,0-4,0% C, 2,0-4,5% B, 0,5-3,5% Si, 6,0-15,0% Cr, 1, 5-7,5% Mo, 6,0-14,0% V, 0-3,0% W, 0-1,5% Mn, 0-2,0% Cu, 2,0-7,0% Ni, залишок - Fe та домішки. Сплав застосовували для внутрішнього наплавлення твердим сплавом металевих циліндрів відцентровим литтям або гарячим ізостатичним пресуванням.
Патент Канади СА 2416950 А1 розкриває матеріал для виготовлення деталей та засобів для застосування при підвищеній температурі, що містить сплав на основі заліза,що включає C, Si, Mn, Cr, Ni та N у певних концентраціях. Сплав утворений холодним штампуванням до твердості щонайменше 230 НВ.
Однак залишаються дві проблеми з такими металами на основі Fe. Перша: зносостійкість цих сплавів на основі Fe все ще гірше за сплави на основі Ni з WC. Щоб бути ближчими до тих властивостей, в основному сплаві потрібно застосовувати дорогі сплавляючі елементи, такі як W, Nb, або додавати великі кількості WC частинок. Ці сплавляючі елементи збільшують ціну і роблять матеріал дуже твердим (більш ніж 65 HRC), що призводить до додаткової обробки та проблем застосування з розтріскуванням. Друга: матеріали на основі Fe не мають хорошу корозійну стійкість, такий як сплави на основі Ni, особливо в змішаних корозійних середовищах.
Мета цього винаходу
Отже, метою даного винаходу є забезпечення альтернативного матеріалу нижчої вартості, який підходить для утворення деталей або покриттів, що володіють високою зносостійкістю і високою хімічною стійкістю.
Ціль досягли за допомогою матеріалу, що включає сплав, що містить від 13 до 16 вагу. відсотків нікелю (Ni), від 13,5 до 16,5 вага. відсотків хрому (Cr), від 0,5 до 3 вага. відсотків молібдену (Mo), від 3,5 до 4,5 вага. відсотків кремнію (Si), від 3,5 до 4 вагу. відсотків бору (B), від 1,5 до 2,1 вага. відсотків вуглецю (C) та від 0,2 до 0,5 вагу. відсотків міді (Cu), залишок – залізо (Fe).
Виявили, що такі сплави на основі заліза з C, B, Cr, Ni, Si і Mo виявляють високу зносостійкість і напрочуд високу хімічну стійкість.
Матеріал містить сплав на основі заліза з додатковими компонентами C, B, Cr, Ni, Si та Mo. Матеріал включає чистий сплав та покриття з композицією сплаву.
Сплавмістить тільки C, B, Cr, Ni, Si та Mo як основні компоненти, крім основного компонента Fe. Зазвичай сплав містить сліди або незначні кількості інших елементів, які є звичайними домішками. Менш переважно, сплав може містити інші елементи в концентраціях, які суттєво не змінюють його хімічну поведінку. Такі факультативні добавки називаються елементами, що супроводжують.
Сплав застосовується для утворення або покриттів на металевій підкладці, або для виробництва формованих продуктів, відлитих продуктів, покриттів, деталей, покритих деталей, дротів, електродів або порошків.
В основному сплав містить 13-16 вагу. відсотків (вага.%) нікелю (Ni), 13,5-16,5 вага. відсотків хрому (Cr), 0,5-3 вага. відсотків молібдену (Mo), 3,5-4,5 вага. відсотків кремнію (Si), 3,5-4 вага. відсотків бору (B) та 1,5-2,1 вагу. відсотків вуглецю (C), залишок - залізо (Fe) та можливі домішки.
Зазвичай домішки є і взагалі неминучі. Вміст домішок у сплаві зазвичай менш ніж 1 вага. відсоток, переважно менш ніж 0,5 вага. відсотка і найбільш переважно менш ніж 0,2 вага. відсотки. Усі згадані вагові відсотки ґрунтуються на вазі всієї композиції, яка становить 100 вагу. відсотків. Усі числові значення є приблизними значеннями.
Переважна композиція сплаву включає від 13 до 14 вагу. відсотків нікелю (Ni), від 14 до 16 вагу. відсотків хрому (Cr), від 1 до 3 вага. відсотка молібдену (Mo), від 3,5 до 4,5 вага. відсотків кремнію (Si), від 3,5 до 4 вагу. відсотків бору (B), від 1,8 до 2,1 вага. відсотків вуглецю (C) та від 0,2 до 0,5 вагу. відсотків міді (Cu), залишок - залізо (Fe) та можливі домішки.
Сплав має незвичайну хорошу корозійну стійкість у змішаних корозійних умовах, дебільшість зносостійких матеріалів на основі Ni або Fe на основі не відповідають. Примітно, що сплав на основі Fe не містить додавання інших твердих частинок збільшення своєї твердості, таких як карбід вольфраму (WC).
Зазвичай сплави мають твердість у діапазоні від 35 HRC до 60 HRC, зокрема в діапазоні від 55 HRC до 60 HRC, типово приблизно 58 HRC, що є надзвичайно низьким для такого зносостійкого матеріалу. Це дає перевагу в обробці та експлуатації, оскільки це робить сплав менш чутливим до розтріскування.
У цьому документі одиниця "HR" є так званою "твердістю за Роквеллом". Існує кілька шкал Роквелла для різних діапазонів твердості. Найзагальнішою є шкала B (HRB), яка підходить для м'яких металів, та шкала C (HRC) для твердих металів. Спосіб для вимірювання твердості за Роквеллом передбачений DIN EN ISO 6508-ASTM Е-18. Числа твердості за Роквеллом не пропорційні даним твердості за Віккерсом, але існують таблиці перетворення, згідно з якими вищезгаданий діапазон від 35 до 60 HRC відповідає твердості за Віккерсом від 345 до 780 HV/10.
Сплави зазвичай мають точку плавлення в діапазоні від 1000 до 1150°C, типово приблизно 1080°C. Це дуже низька температура плавлення для такого сплаву з цими властивостями, яка знижує вартість при обробці і дає перевагу в застосуванні.
Сплав отримують зазвичай плавленням компонентів або змішуванням порошків або сполук.
Сплав можна відлити у продукти будь-якої форми.
Сплав застосовують для виробництва деталей або покриттів на деталях, які є металевими підкладками або металевими деталями, особливо виготовленими зі сталі. Металевими деталямиє, наприклад, ротори, втулки, опори, болти, леза тощо.
Матеріал, зокрема сплав, переважно застосовують для виробництва дротів, присадочних дротів, стрічок, продуктів у формі ниток, електродів, порошків, паст, суспензій або матеріалу литої заготівлі, які застосовують, наприклад, для лиття, зварювання, плазмового зварювання (РТА), плазмового наплавлення порошку або дугового зварювання, паяння твердим припоєм, газоплазмового напилення, зокрема високошвидкісного газоплазмового напилення (HVOF), сплавлення спіканням та подібних способів.
Даний винахід також містить спосіб нанесення матеріалу за даним винаходом для виробництва покриттів з високим рівнем стійкості до корозії та зносу на виріб термічним процесом покриття, в якому матеріал покриття у формі порошку сплавлений і розпорошений з розплаву або агломерований з різних сплавлених і несплавлених металевих порошків.
Покриття або захисні шари сплаву на деталях, зокрема металевих деталях, отримані переважно загальноприйнятими способами нанесення порошку заливкою, виливком, зануренням, розпиленням, видавлюванням з подальшою обробкою термічним сплавленням або термічними способами, такими як газоплазмове напилення F , або зварили плазмовим зварюванням. Такі способи покриття описані, наприклад, патент США №№6187115 А і 6322857 А, які можна застосовувати аналогічно і які включені посиланням.
Такі покриття можна отримати, як згадано вище, термічними процесами, застосовуючи матеріали, що містять сплав, такі як порошки, дроти, електроди або інші звичайні форми або нанесенням двох або більше матеріалів, які відхиляються в композиції від отриманого в результаті готовогосплаву, де матеріали відокремлені або змішані, наприклад, різні електроди або змішані порошки, приводячи в результаті покриття з композицією сплаву.
Такі покриття або захисні шари служать для отримання захисту від зношування та корозії в хімічній промисловості, фармацевтичній промисловості, паперовій промисловості, скляній промисловості, енергетичній промисловості, цементній промисловості, переробці відходів, целюлозно-паперовій промисловості та промисловості обробки пластмаси. Покриті деталі також застосовують переважно для застосування в розробці нафти та газу.
Зазвичай покриття мають товщину в діапазоні від 01 до 20 мм, переважно від 1 до 10 мм.
Детальний опис кращих варіантів здійснення
Даний винахід буде більш докладно пояснено з посиланням на варіант здійснення і графічний матеріал, який показаний детально.
Фіг.1 є діаграмою ступеня втрати об'єму стандартизованому випробуванні на абразивний знос (ASTM G65) в залежності від композиції сплаву,
Фіг.2 є діаграмою ступеня втрати ваги стандартизованому випробуванні на корозію при контакті з HCl залежно від вмісту Ni в сплаві Х5; і
Фіг.3 є діаграмою ступеня втрати ваги стандартизованому випробуванні на корозію при контакті з HNO3 в залежності від вмісту Ni в сплаві Х5.
Приклад 1 (Зразок Х5)
Серію сплавів приготували сплавленням металевих елементів та з'єднань у розплав та утворенням двох порошків, які представлені в таблиці 1 нижче: