СИРОВЕ ВІДДІЛЕННЯ - Технологія виробництва цементу ЗАТ - Нев’янський цементник
Дроблений вапняк, висушена глина, пісок і недогарки через вагові дозатори у заданому відсотковому співвідношенні надходять на систему збірних (головних) стрічкових конвеєрів (B = 1600 мм, L1 = 87 м, L2 = 127 м, L3 = 11,5 м). Утворена таким чином сировинна шихта надходить у розподільчий бункер - "штани", всередині якого знаходиться розподільник. Регулюючи положення розподільника можна подавати сировинну суміш на один, на інший або на обидва стрічкові живильники (B = 1000 мм, L = 3,4 м), які живлять сировинні млини (4,2 10 м), що працюють у замкнутому циклі з прохідними сепараторами D = 5,5 м-коду.
Барабанний сировинний млин розмірами 4,2 10 м призначений для тонкого помелу сировинних компонентів і одночасного їх підсушування.
Барабанний млин є горизонтально розташований барабан, частково заповнений тілами, що мелють (кулі, стрижні).
Матеріал у млині подрібнюється в основному за рахунок ударної роботи падаючих тіл, що мелють, при незначній роботі тертя. При обертанні млина тіла, що мелють, під дією відцентрової сили притискаються до внутрішньої стінки корпусу і піднімаються на певну висоту, під дією сили тяжіння відриваються від корпусу і при падінні розбивають шматки матеріалу, які безперервно надходять через завантажувальну цапфу. Подрібнений матеріал безперервно виходить в іншому кінці млина.
Барабанні млина залежно від схеми помелу розрізняють відкритого чи замкнутого циклу. Помел по замкнутому циклу характеризується тим, що млин працює у поєднанні з класифікатором – сепаратором. В цьому випадку в млині не закінчується помел всього поданого до неї матеріалу до заданої кінцевої тонкощі. Відбір частинок заданого розміру проводиться сепаратором, а млин подрібнюєматеріал лише для сепарації. Весь матеріал, що виходить з млина, як великий, так і дрібний, проходить через сепаратор, в якому відбувається відділення матеріалу заданої тонкощі помелу. Великі зерна із сепаратора повертаються до млина для помелу.
Перед помелом сировинні матеріали висушують у сушильних барабанах. Вологість матеріалів, що подаються до млина, при сухому помелі не повинна перевищувати 5 %. Корпус млина виготовлений із сталевих листів завтовшки до 40 мм. З торцевих сторін корпус закритий днищами, відлитими разом з пустотілими цапфами, якими млин спирається на підшипники цапфові ковзання. Завантажувальна частина млина (рис. 7) складається з тічки 1, за якою матеріал надходить у завантажувальний патрубок 2, виготовлений з листової сталі і прикріплений болтами до торця завантажувальної цапфи і обертається разом з нею. У цьому патрубку розташовані радіально лопаті, призначені для подачі матеріалу в цапфу. В останню вставлена і закріплена нерухомо сталева втулка 3, що має гвинтові лопаті 4 для просування матеріалу в барабан.
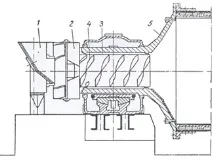
Мал. 7.Схема завантажувальної частини барабанного млина: 1 - течка; 2 – патрубок; 3 – сталева втулка; 4 - гвинтові лопаті; 5 - поверхня днища.
Ця втулка оберігає цапфу від зносу і торцевою стороною примикає до футерування внутрішньої поверхні днища 5.
На одному кінці млина жорстко закріплено вінцеву шестерню. Млин наводиться у обертання безредукторним електродвигуном потужністю 2000 кВт, частота обертання 100 об/хв. Частота обертання млина 15,6 об/хв. Привід виконаний за схемою: двигун – промвал – зубчаста відкрита пара.
Тілі тіла - кулі - бувають литими, кованими або штампованими. Виготовляють їх з вуглецевої, марганцовистої та хромистої сталі.
Млин завантажується кулями діаметром 40 – 80 мм. Асортимент завантаження: 40 мм – 12 т; 50 мм – 18 т; 60 мм – 18 т; 70 мм – 36 т; 80 мм - 36 т. Всього 120 т. Коефіцієнт заповнення тілами, що мелють 0,2.
Розміри тіл, що мелють, змінюють в залежності від роду подрібнюваного матеріалу. Чим більше зерна матеріалу, що надходить до млина, тим більшими повинні бути кулі. Середній діаметр тіл, що мелють, зменшується по ходу руху матеріалу. Наприкінці камери велике значення має процес стирання, тому туди завантажують цільпебси. Витрата тіл, що мелють - 0,04 кг/т сировини.
Постійний режим роботи млина забезпечується періодичним, через кожні 100 - 200 год, довантаженням тіл, що мелють, а через 1800 - 2000 год - повним їх перевантаженням.
Тілі тіла в процесі помелу матеріалу класифікуються: більші переміщаються до розвантажувального кінця кожної камери, а дрібніші - до завантажувального. Це явище несприятливо позначається на роботі млина, оскільки матеріал у міру подрібнення повинен розмелюватися дрібнішими кулями. Цей недолік усувається застосуванням класифікуючих бронефутерувань полочного типу, конусно-ступінчастих з каблучковою поверхнею.
Бронева футеровка оберігає внутрішні поверхні барабана млина від зносу, а також чинить опір руху тіл, що мелють. Довжина броньових плит 250 – 500 мм, ширина 300 – 400 мм, товщина 50 – 110 мм, маса до 80 кг.
Робоча поверхня броньових плит буває плоскою, рифленою, хвилястою, ребристою та ступінчастою. Залежно від профілю розрізняють циліндричні та конусні плити (стосовно осі млина).
Броневі плити з каблучковою поверхнею виготовляються з аустенітової сталі. Вони в кілька разів зносостійкіші, ніж бронеплити з вуглецевої сталі. Розміри підборів тавідстань між ними вибираються відповідно середньому діаметру куль з таким розрахунком, щоб між ними не могли заклинюватися найдрібніші з куль, що завантажуються в камеру. Підбори можна розміщувати паралельними рядами або у шаховому порядку. У млині з такою футеровкою тіл, що мелють, не ковзають по броньових плитах. Броневі плити, що автоматично сортують мелючі кулі, монтуються всередині млина кільцями так, що поверхня кожного кільця, що мелє, розташовується під кутом до центральної осі барабана.
Конусно-ступінчасте бронефутерування утворює набір коротких усічених конусів, звернених вершиною у бік розвантажувальної частини. У млині з такою футеровкою більші і важкі кулі, що мелють, збираються біля завантажувального кінця, а дрібні, легші переміщаються до розвантажувального кінця. Завдяки цьому відпадає необхідність у перегородках усередині млина.
Плити надійно кріплять до барабана млина болтами, які виготовляють з м'якої сталі, що забезпечує ретельність їх нарізування.
Для зниження шуму між корпусом та плитами укладають гумові прокладки.
Помел сировини проводиться одночасно з його підсушуванням газами, що відходять від обертової печі, з температурою 250 0 С.
З розвантажувального кінця млина сировинне борошно виноситься газами в повітряно-прохідний сепаратор, що працює в замкнутому циклі із сировинним млином.
Поділ частинок матеріалу за крупністю та об'ємною вагою заснований на різниці швидкостей, з якою частинки випадають з повітряного потоку.
У повітряно-прохідному сепараторі з повітряного потоку вловлюються та осаджуються лише великі частинки матеріалу (крупка). Дрібні частки уловлюються в циклонах, куди прямує запилене повітря із сепаратора.
Повітряно-прохідний сепаратор (рис. 8) складається зкожухів 2 і 3. Повітря з вихідним матеріалом надходить по патрубку 1 корпус сепаратора 2. Через розширення каналу, в якому рухається суміш, швидкість потоку падає і великі частинки випадають із суміші під дією сили тяжіння. Дрібні частинки проходять разом з повітрям по напрямних лопатках 4 у внутрішній конус 3, де потік закручується і з нього випадають частинки середньої крупності в результаті на них відцентрових сил. Великі частинки відводяться з сепаратора по патрубках 6, а дрібні виносяться трубою 5 в осадитель. Кордон розділення регулюється дроселюванням вхідного потоку або шляхом зміни кута повороту лопаток 4.
Мал. 8.Схема повітряно-прохідного сепаратора: 1 - патрубок; 2 – кожух зовнішній; 3 - кожух внутрішній; 4 - напрямні лопатки; 5 – труба; 6 - патрубки
Одержуване сировинне борошно осідає в циклонах D = 2,35 м (8 шт.). Вона має вологість менше 1%. Тонкість помелу характеризується залишком на ситі № 02 та 008, який становить 1 та 10 %. Продуктивність установки – 130 т/год.
Повітря просмоктується через установку за допомогою димососа ДЦ-25 2, надходить в електрофільтр ЕГА 1 - 40 - 12 - 6 - 4, який у свою чергу просмоктується димососом ДРЦ-21 2. Очищені гази викидаються в атмосферу трубою 4,2 120 м. Розрідження перед млином – 500 МПа, за млином – 4500 МПа, за сепаратором – 4800 МПа. Температура газів перед млином – 160 0С, за млином – 65 0С.
Після осадження сировинне борошно збирається в бункері і за допомогою пневмокамерних насосів ТА - 28 (П = 130 т/год) по трубопроводу подається в двоярусні силоси (D = 18 м, H = 60 м, V = 7850 м3, V = 8000 т) , призначені для зберігання, гомогенізації та усереднення сировинного борошна. Нижній ярус силосу виконаний у вигляді залізобетонного циліндра,верхній - із залізних царг.
Верхній силос – змішувальний (D = 17,6 м, H = 12 м, V = 1750 м3, V = 2000 т).
У кожному змішувальному силосі та співвісно з ним розташована металева циліндрична камера 6 10 м, корисна місткість якої до 230 т борошна. У нижній частині камера жорстко пов'язана з днищем силосу, а у верхній - за допомогою чотирьох горизонтальних і радіально розташованих труб розпорів так само з'єднана зі стінкою силосу. Верх камери відкритий, а в нижній частині є вісім прохідних отворів 800-400 мм.
По центру силосу змонтовано вертикальну переливну (вивантажувальну) трубу діаметром 1000 мм із звуженням на виході із змішувального силосу до 600 мм, яке виходить через перекриття в нижче розташований залізобетонний запасний силос зовнішнім діаметром 18 м.
На днищах силосу та камери є 112 аерокоробок, кожна з яких має коритоподібний штампувально-зварний корпус з рядом поперечних перегородок, що утворюють у коробці ряд ізольованих один від одного відсіків. По осі корпусу розміщена перфорована трубка з рядом розрахункових отворів для пропуску стиснутого повітря певної кількості.
Для більшої інтенсифікації процесу усереднення борошна під обрізами матеріалопроводів Ш 300 мм розташовані спеціальні відбійні сталеві пластини з конусом для створення кільцеподібного струменя матеріально-повітряної суміші, що виходить із трубопроводу зі швидкістю 20 - 30 м/с. Струмінь суміші з такою швидкістю, інтенсивно впроваджуючись в раніше замелене сировинне борошно, практично миттєво усереднює її.
При періодичному режимі гомогенізації під час перемішування працює кожен силос один свій великий нагнітач, а період вивантаження - той самий великий чи малий нагнітач. Два інших (великий і малий) нагнітача знаходяться врезерві. Великі та малі нагнітачі встановлені в окремому приміщенні відділення сировинних млинів, що примикає до двоярусних гомогенізаційних силосів.
Відмінною особливістю конструкції змішувальних силосів є те, що в них подача стисненого повітря від нагнітачів проводиться одночасно у всі аерокоробки, що знаходяться в силосі. Причому розподіл його у певних кількостях по окремих аерокоробках або навіть відсіках в них здійснюється примусово під натиском за рахунок наявності строго розрахункового діаметра та кількості отворів у повітропровідних перфорованих трубках і в корпусах аерокоробок.
Аспірація змішувальних та запасних силосів здійснюється за допомогою двох рукавних фільтрів, оснащених двома аспіраційними вентиляторами. Аспіраційне обладнання розміщується в міжярусному просторі на позначці + 43,00 м, уловлений пил з рукавних фільтрів безперервно розвантажується по тічках в запасні силоси, що знаходяться нижче.
Коригування сировинної суміші провадиться по титру.
Сировинний силос напрацьовується на ѕ, після чого відбирається проба і проводиться її експрес-аналіз з визначенням титру. Після цього на дозатори сировини оператором подається сигнал дозування компонентів відповідно до внесеними коригуваннями.
Після того, як суміш відкоригована та гомогенізована, вона скидається у нижній силос, де зберігається (D = 18 м, H = 28 м, V = 6100 м3, V = 6000 т). Загальна місткість двох силосів дозволяє мати запас сировинного борошна, що забезпечує роботу печі протягом 3,3 діб.
Система аерації верхнього силосу виконана в такий спосіб, що гомогенізація може здійснюватися як періодично, а й безперервно. Система гомогенізації сировинного борошна здатна за періодичного режиму роботи забезпечуватиступінь усереднення сировинного борошна від 5 до 18, а при безперервному режимі - 4. Подача повітря в систему аерації проводиться турбонагнітачами ЦНО - 3 - 12000 м3/год.
Нижній силос є запасним, і його розпушувальна система розрахована на аерацію для забезпечення рівномірного та повного вивантаження сировинного борошна із силосу. Стиснене повітря для аерації запасних силосів подається від центральної компресорної. З запасних силосів сировинне борошно пневмодозуючими установками подається у видаткові бункери вузла живлення печі.
Відділення працює безперервно за двозмінним графіком. Собівартість 1 т сировинного борошна близько 102,3 руб.